Production and Component Behaviour
Head of the group
Scientific Staff
Dr.-Ing. Frauke Hinrichs
M.Sc. Niki Nouri
M.Sc. Philipp Schüßler
M.Sc. Benjamin Dollhofer
M.Sc. Moritz Klug
M.Sc. Christian Krämer
M.Sc. Mehdi Khabou
M.Sc. Pierre Gast
Competence
In the framework of the research of the group "Production and Component Behaviour" the interactions between production processes, component state and component behaviour at mechanical loading are investigated. The goal of the investigations is to adjust the production process in such a way that an optimal component condition is achieved. The production processes considered are available either in the laboratories of production techniques of IAM-WK or within cooperation with institutes of production sciences. They are subdivided into the main groups of production processes according to DIN as follows:
Forming
- Additive Manufacturing
- Casting
Cutting
- High Speed Cutting
- Micromachining, Microerosion
- Laser ablation
Chaning materials properties
- Hardening and tempering of steels
- Case hardening of steels
- Inductive heat treatment
- Laser beam hardening
- Shot peening
- Deep rolling
An essential focus of the work of the department " Production and Component Behavior" is the characterization of production-related component and material states. For this purpose, the central laboratories of Materialography and X-Ray Laboratory at IAM-WK are used to gain an insight into the microstructure, the residual stress state and defect structures.
In addition, facilities of the heat treatment laboratory and the laboratories for mechanical testing are used to determine the stability of the surface layer conditions under thermal, quasi-static, cyclic and combined loads. Furthermore, in the laboratories for mechanical testing, the effects of production-related component states on the strength, in particular the fatigue strength, of metallic and ceramic materials are investigated together with the department "Fatigue Strength".
An additional important main subject of the research of the section "Production and Component Behaviour" is the Simulation of the generation of production induced component states at different production steps. Here, different Finite-Element-Programs (Numerical Simulation) are used to describe especially thermo-mechanically coupled processes, if necessary including phase transformations. The necessary input data are determined experimentally (Laboratory of production techniques).
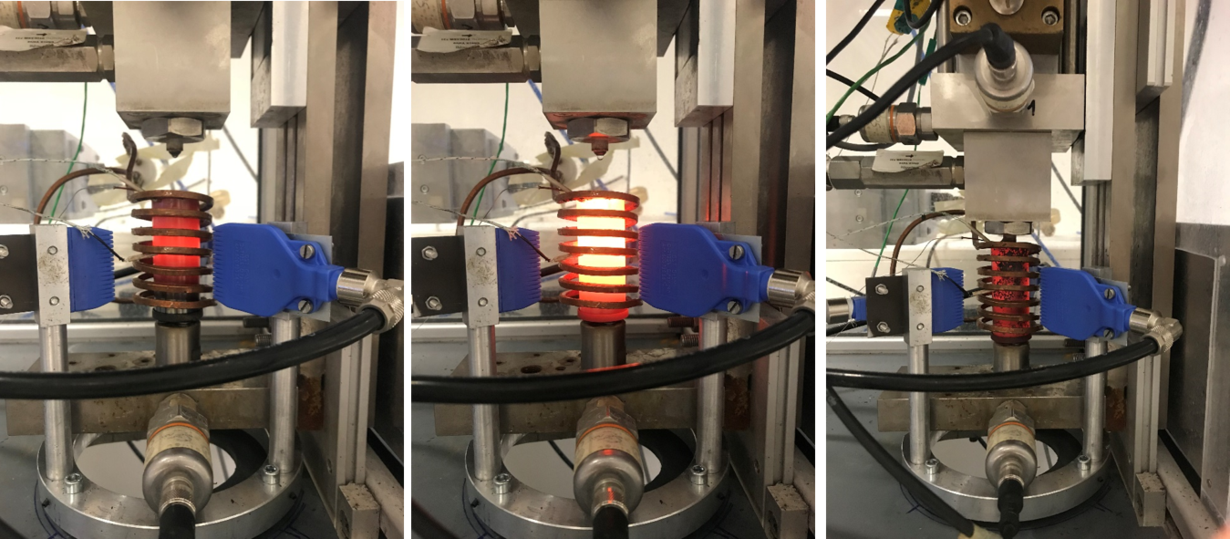
Heat treatment from the main group "Changing material properties" includes processes or process chains for thermal, thermo-chemical and thermo-mechanical treatment of workpieces. The component properties, which are important in many applications, are adjusted by specific heating and cooling phases and the resulting phase transformations via the microstructure composition, the residual stress state and the hardness. In heat treatment, a fundamental distinction is made between processes that cause a radical structural transformation and processes that only cause a transformation on the surface of a workpiece. The first-mentioned processes include annealing and hardening, i.e. thermal processes. The second-mentioned processes count as diffusion and coating processes as well as thermochemical processes. The thermochemical surface hardening processes are mainly characterised in series production by a significant increase in surface hardness and lifetime at low unit costs. On the one hand, it is intended to achieve high surface layer hardness in order to minimize the wear. On the other hand, the microstructure and residual stress depth profiles are specifically adjusted, which usually leads to an extension of the durability. The current research focus is the optimization of heat treatment processes for components that are difficult to access. The adjustment of mixed microstructures to improve the mechanical properties is another important aspect. The goal is to improve fatigue properties compared to the conventional quenching and tempering processes by adjusting different microstructure components.
more
Mechanical surface treatment comprises a number of processes from the main manufacturing group "Modification of material properties", which are used to improve the component behaviour under operational loads. Mechanical surface treatments include, for example, shot peening, deep rolling, machine hammer peening, and some other processes that are used in customized industrial applications. The mechanical surface treatment of a component causes plastic deformation of its surface layer, resulting in local work hardening and the formation of residual compressive stresses. In particular, the processes deep rolling and machine hammer peening can also be used to smooth and structure surfaces due to their deterministic nature. A combination of smooth surface, work hardening and residual compressive stresses is particularly advantageous for improving the service life properties in the fatigue stress frequently encountered in mechanical, automotive and aircraft engineering. Structured surfaces, such as bionic ones, can also be created to optimize wear behavior. The focus of the research work in the department "Manufacturing and Component Behavior" is on the new and further development of processes, the identification of the relationships between process parameters, surface layer characteristics and component behavior, as well as numerical process simulation and modeling for the prediction of surface layer properties and component behavior. Furthermore, we deal with thermomechanical surface treatments, such as shot peening at elevated temperature or machine hammer peening under cryogenic conditions. Also in the context of additive manufacturing, mechanical surface treatments are used as final processes or processes switched within the build-up to optimize surface layer and component properties. This illustrates the intensive interdependence of the issues considered within the department "Production and component behaviour".
more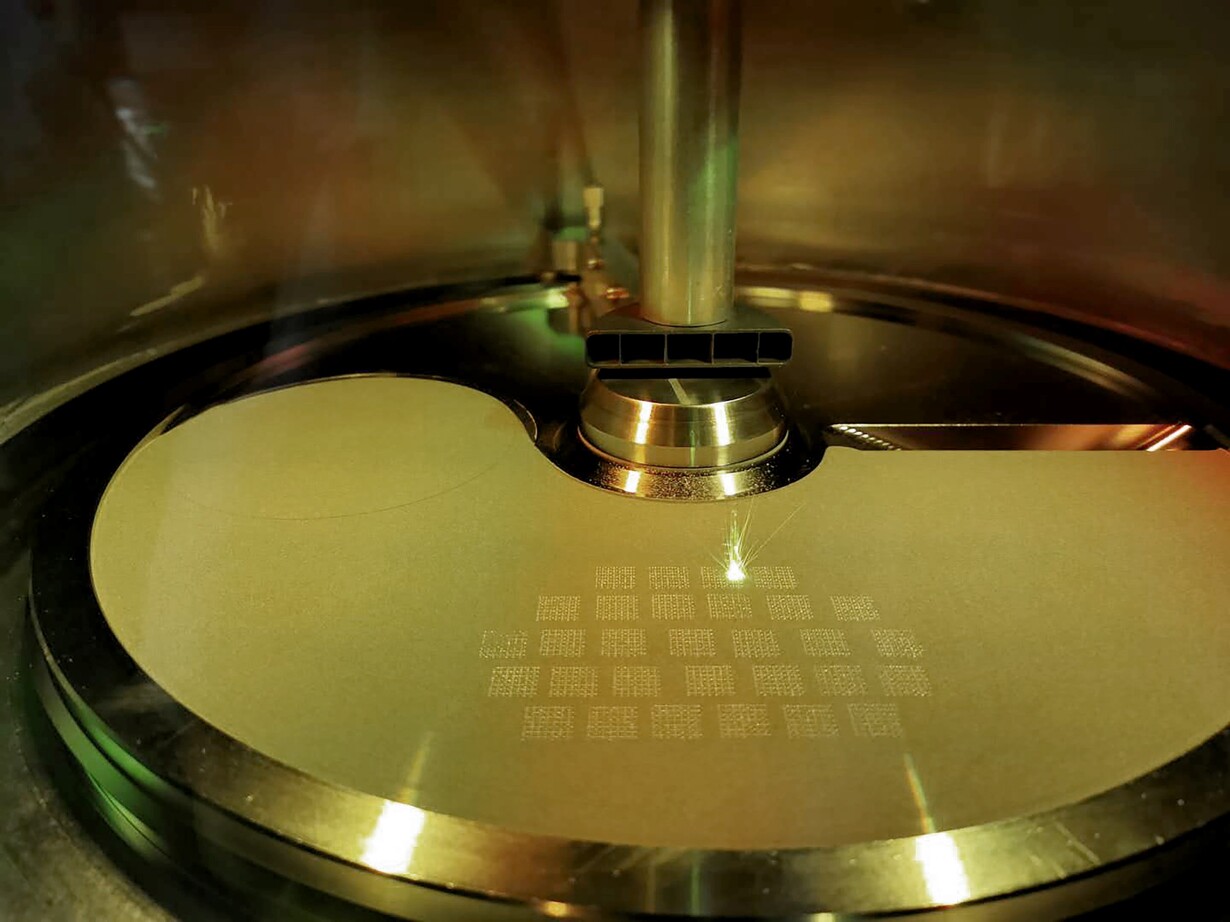
Additive manufacturing (AM) is characterized, in comparison to conventional manufacturing processes, by the layer-wise build-up of the three-dimensional shape of the component directly from the CAD geometry. Basic materials are metal powder, metal or polymer filaments as well as resins and inks which are consolidated by energy input or chemical cross-linking. The main energy sources used today are laser or electron beams and electrically or inductively heated extrusion heads. Due to the direct production of the component without geometry-bound tools or moulds, additive manufacturing plays a pioneering role, especially in the field of advanced manufacturing. The continuous digitalization and automation of the process chain, the products with high design complexity as well as the possibility of function integration enable additive manufacturing to be used more and more intensively as an innovative technology in various applications. Due to the layered build-up with a specific exposure or deposition strategy of the base material, additive manufactured components not only have a characteristic microstructure but also process-related defects (pores, voids, cracks). The knowledge of the underlying causes in connection with the process control as well as the effect on component properties and component behaviour is fundamental for the application of additively manufactured structural components. At the same time, the highly localised process zone (e.g. in the melt pool or during filament extrusion) offers the possibility of controlling the microstructure and defect structures in a targeted manner. This requires precise control of the temperature history and the exposure/deposition strategy from the melt pool via the individual layer to the entire component. Due to these complex dependencies in the process-structure-property relationships, especially the reproducibility and testing of additively manufactured components is still a largely open field of research.
more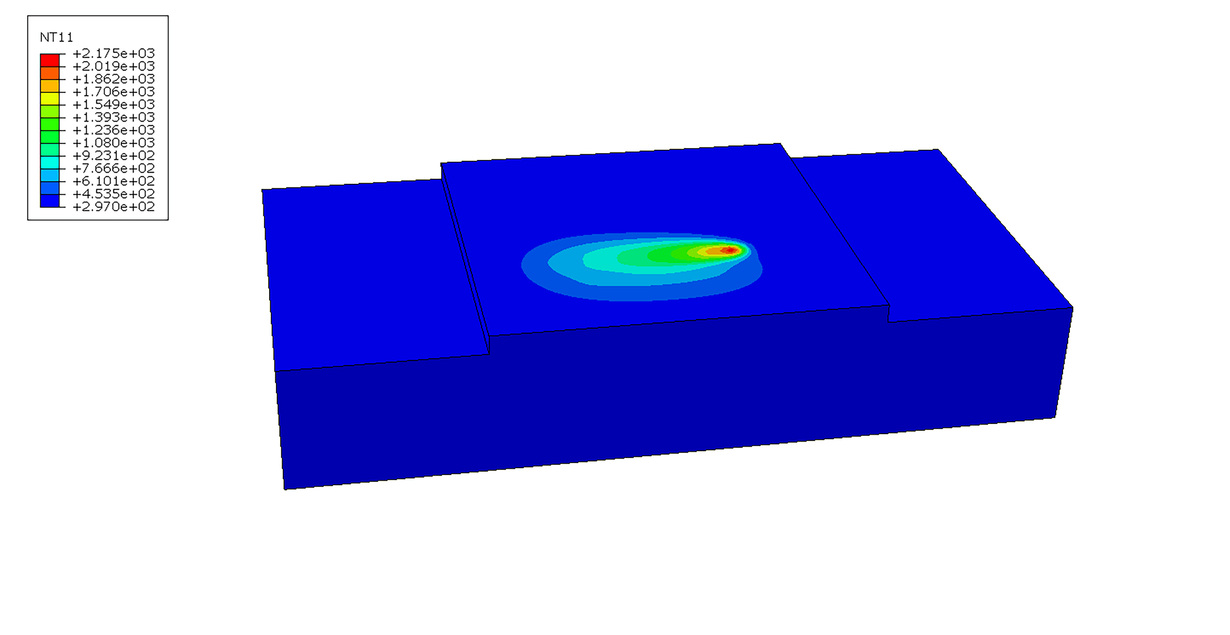
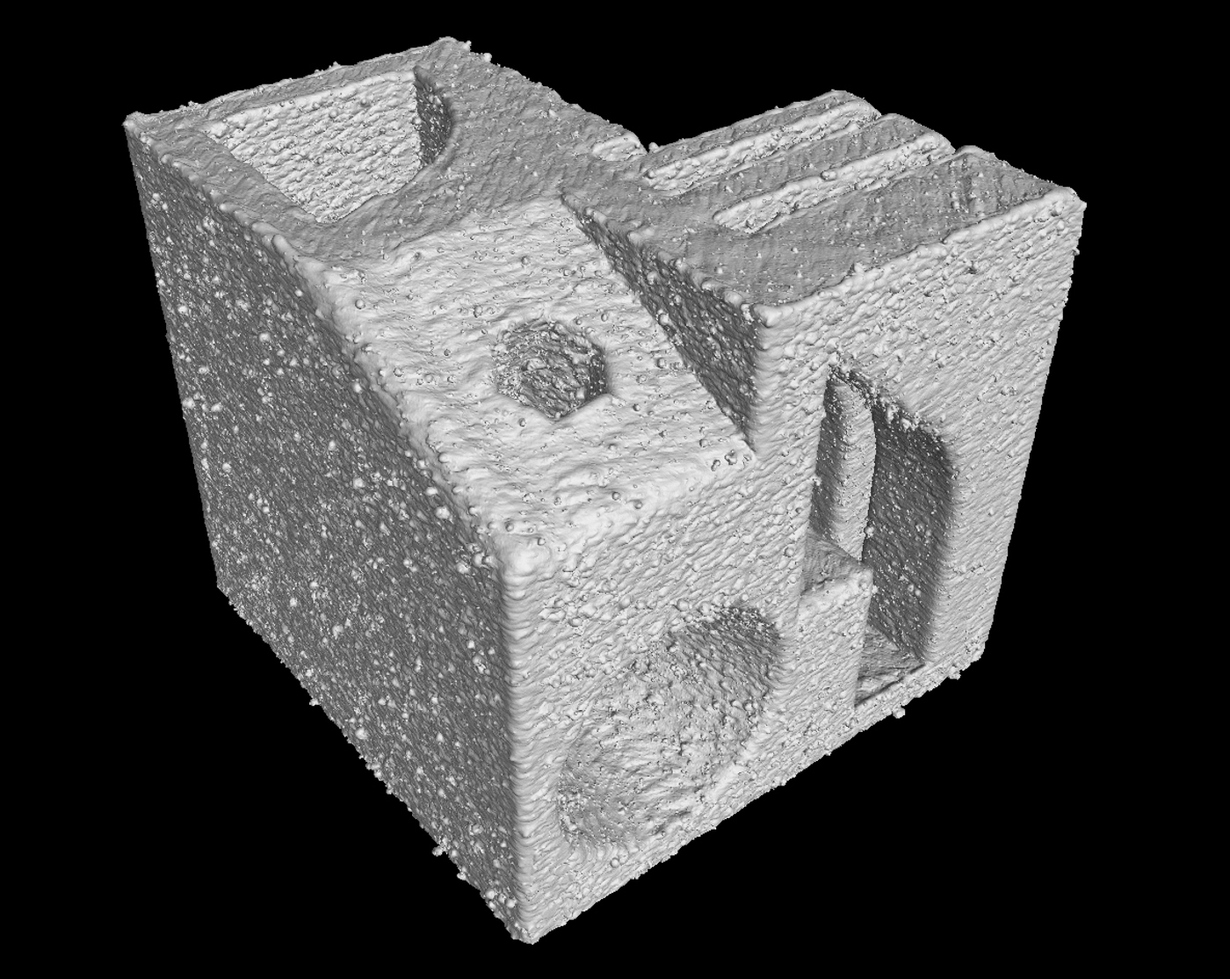
Publications
Klug, M.; Sen, S.; Dietrich, S.; Schulze, V.
2025. QDE 2025: Proceedings of the 3rd International Conference on Quenching and Distortion Engineering, 58–67, ASM International. doi:10.31399/asm.cp.qde2025p0058
Nouri, N.; Lapouge, P.; Dirrenberger, J.; Dietrich, S.; Schulze, V.
2025. QDE 2025: Proceedings of the 3rd International Conference on Quenching and Distortion Engineering, 42–50, ASM International. doi:10.31399/asm.cp.qde2025p0042
Schüßler, P.; Dollhofer, B.; Krämer, C.; Englert, L.; Hinrichs, F.; Schulze, V.; Dietrich, S.
2025. Journal of Materials Research and Technology, 35, 1358–1368. doi:10.1016/j.jmrt.2025.01.073
Schüßler, P.; Schulze, V.; Dietrich, S.
2025. Solid Freeform Fabrication Symposium, 818–826, University of Texas at Austin. doi:10.26153/tsw/58117
Krämer, C.; Schulze, V.; Dietrich, S.
2025. QDE 2025: Proceedings of the 3rd International Conference on Quenching and Distortion Engineering, May 6–7, 2025, Vancouver, Canada, 51–57, ASM International. doi:10.31399/asm.cp.qde2025p0051
Schüßler, P.; Schulze, V.; Dietrich, S.
2025. QDE 2025: Proceedings of the 3rd International Conference on Quenching and Distortion Engineering, 68–77, ASM International. doi:10.31399/asm.cp.qde2025p0068
Nouri, N.; Hillenmeyer, E.; Thavarajan, T.; Dietrich, S.; Schulze, V.
2025. Journal of Materials Research and Technology, 34, 730–737. doi:10.1016/j.jmrt.2024.12.042
Meyer, S.; Englert, L.; Schüßler, P.; Schulze, V.; Dietrich, S.
2024. Progress in Additive Manufacturing. doi:10.1007/s40964-024-00899-0
Englert, L.
2024, December 10. Karlsruher Institut für Technologie (KIT). doi:10.5445/IR/1000177107
Nouri, N.; Graf, G.; Sen, S.; Schulze, V.; Dietrich, S.
2024. Netsu-shori = Heat treatment, 64, 17–22. doi:10.14940/netsushori.64.ex17
Dollhofer, B.; Krämer, C.; Nouri, N.; Dietrich, S.; Schulze, V.
2024. Proceedings of the 29th International Federation for Heat Treatment and Surface Engineering World Congress (IFHTSE 2024), 41–49, ASM International. doi:10.31399/asm.cp.ifhtse2024p0041
Nouri, N.; Dietrich, S.; Schulze, V.
2024. Proceedings of the 29th International Federation for Heat Treatment and Surface Engineering World Congress (IFHTSE 2024), 50–56, ASM International. doi:10.31399/asm.cp.ifhtse2024p0050
Grauberger, P.; Dörr, M.; Lanza, G.; Kaiser, J.-P.; Albers, A.; Düser, T.; Tusch, L.; Seidler, M.; Dietrich, S.; Schulze, V.; Matthiesen, S.
2024. at - Automatisierungstechnik, 72 (9), 815–828. doi:10.1515/auto-2024-0010
Sen, S.; Mayer, D.; Fischer-Bühner, J.; Beckers, D.; Schubert, J.; Dietrich, S.; Kauffmann, A.; Zanger, F.
2024, September 25. Materials Science and Engineering Congress (MSE 2024), Darmstadt, Germany, September 24–26, 2024
Heizmann, M.; Beyerer, J.; Dietrich, S.; Hoffmann, L.; Kaiser, J.-P.; Lanza, G.; Roitberg, A.; Stiefelhagen, R.; Stricker, N.; Wexel, H.; Zanger, F.
2024. at - Automatisierungstechnik, 72 (9), 829–843. doi:10.1515/auto-2024-0009
Englert, L.; Schulze, V.; Dietrich, S.
2024. NDT & E International, 146, Art.-Nr.: 103166. doi:10.1016/j.ndteint.2024.103166
Stebner, S. C.; Martschin, J.; Arian, B.; Dietrich, S.; Feistle, M.; Hütter, S.; Lafarge, R.; Laue, R.; Li, X.; Schulte, C.; Spies, D.; Thein, F.; Wendler, F.; Wrobel, M.; Vasquez, J. R.; Dölz, M.; Münstermann, S.
2024. Advances in Industrial and Manufacturing Engineering, 8, 100133. doi:10.1016/j.aime.2023.100133
Dittmann, K.; Czink, S.; Dietrich, S.; Trauth, A.; Weidenmann, K. A.
2024. 3D Printing and Additive Manufacturing, 11 (2), e537–e547. doi:10.1089/3dp.2022.0118
Shi, C.; Schulze, V.; Dietrich, S.
2024. Materials Science and Technology, 40 (2), 107–119. doi:10.1177/02670836231212614
Schüßler, P.; Nouri, N.; Lapouge, P.; Dietrich, S.; Schulze, V.
2024. Netsu-shori = Heat treatment / Nihon netsu shori gijutsu kyōkai, 64, 72–77. doi:10.14940/netsushori.64.ex72
Dollhofer, B.; Dietrich, S.; Schulze, V.
2024. Netsu-shori = Heat treatment / Nihon netsu shori gijutsu kyōkai, 64, 66–71. doi:10.14940/netsushori.64.ex66
Nouri, N.; Li, Q.; Schneider, R.; Damon, J.; Schüßler, P.; Laube, S.; Müller, E.; Graf, G.; Schulze, V.; Dietrich, S.
2024. Materials Characterization, 207, 113522. doi:10.1016/j.matchar.2023.113522
Schüßler, P.; Franke, J.; Czink, S.; Antusch, S.; Mayer, D.; Laube, S.; Hanemann, T.; Schulze, V.; Dietrich, S.
2023. Materials, 16 (20), Art.-Nr.: 6678. doi:10.3390/ma16206678
Shaji Karapuzha, A.; Fraser, D.; Schliephake, D.; Dietrich, S.; Zhu, Y.; Wu, X.; Huang, A.
2023. Materials Science and Engineering: A, 882, Art.-Nr.: 145479. doi:10.1016/j.msea.2023.145479
Czink, S.; Lubkowitz, V.; Dietrich, S.; Schulze, V.
2023. Additive Manufacturing Letters, 6, 100132. doi:10.1016/j.addlet.2023.100132
Eimer, E.; Ganguly, S.; Czink, S.; Dietrich, S.; Chehab, B.; Ding, J.; Williams, S.
2023. Materials Science and Engineering: A, 880, Artkl.Nr.: 145272. doi:10.1016/j.msea.2023.145272
Damon, J.; Schüßler, P.; Mühl, F.; Dietrich, S.; Schulze, V.
2023. Materials & Design, 230, Artkl.Nr.: 111991. doi:10.1016/j.matdes.2023.111991
Spies, D.; Molitor, D. A.; Damon, J.; Knoll, M.; Dietrich, S.; Schulze, V.; Groche, P.
2023. Material Forming 26th International ESAFORM Conference on Material Forming (ESAFORM 2023) Krakau, Polen, 19.04.2023–21.04.2023, 2081–2090, Materials Research Forum LLC. doi:10.21741/9781644902479-223
Streck, S.; Wiege, T.; Dietrich, S.; Herger, R.; Schulze, V.
2023. Engineering Fracture Mechanics, 284, Art.-Nr.: 109243. doi:10.1016/j.engfracmech.2023.109243
Wang, T.; Meng, K.; Liu, X.; Chen, S.; Zhang, J.; Shi, C.
2023. Advanced Engineering Materials, 25 (10), Art.-Nr.: 2201610. doi:10.1002/adem.202201610
Schüßler, P.; Damon, J.; Mühl, F.; Dietrich, S.; Schulze, V.
2023. Computational Materials Science, 221, Art.-Nr.: 112079. doi:10.1016/j.commatsci.2023.112079
Babinský, T.; Šulák, I.; Kuběna, I.; Man, J.; Weiser, A.; Švábenská, E.; Englert, L.; Guth, S.
2023. Materials Science and Engineering: A, 869, Artkl.Nr.: 144831. doi:10.1016/j.msea.2023.144831
Shi, C.; Nouri, N.; Schulze, V.; Dietrich, S.
2023. International Journal of Fatigue, 168, Article no: 107469. doi:10.1016/j.ijfatigue.2022.107469
Siddharth; Jana, P.; Dietrich, S.; Roy, S.
2023. Materials Science and Engineering: A, 864, Artkl.Nr.: 144614. doi:10.1016/j.msea.2023.144614
Nouri, N.; Graf, G.; Dietrich, S.; Schulze, V.
2023. 28th Congress of the International Federation for Heat Treatment and Surface Engineering, IFHTSE 2023, International Federation for Heat Treatment and Surface Engineering (IFHTSE)
Dollhofer, B.; Dietrich, S.; Schulze, V.
2023. 28th Congress of the International Federation for Heat Treatment and Surface Engineering, IFHTSE 2023, International Federation for Heat Treatment and Surface Engineering (IFHTSE)
Dietrich, S.; Heudorfer, R.; Schulze, V.
2023. 28th Congress of the International Federation for Heat Treatment and Surface Engineering, IFHTSE 2023, International Federation for Heat Treatment and Surface Engineering (IFHTSE)
Schüßler, P.; Nouri, N.; Dietrich, S.; Schulze, V.
2023. 28th Congress of the International Federation for Heat Treatment and Surface Engineering, IFHTSE 2023, International Federation for Heat Treatment and Surface Engineering (IFHTSE)
Austin, A.; Autenrieth, H.; Dietrich, S.; Pundt, A.; Schulze, V.
2023. 28th Congress of the International Federation for Heat Treatment and Surface Engineering, IFHTSE 2023, International Federation for Heat Treatment and Surface Engineering (IFHTSE)
Stebner, S. C.; Martschin, J.; Arian, B.; Dietrich, S.; Feistle, M.; Hütter, S.; Lafarge, R.; Laue, R.; Li, X.; Schulte, C.; Spies, D.; Thein, F.; Wendler, F.; Wrobel, M.; Vasquez, J. R.; Dölz, M.; Münstermann, S.
2023. doi:10.48550/arXiv.2305.19601
Schüßler, P.; Nouri, N.; Schulze, V.; Dietrich, S.
2023. Virtual and Physical Prototyping, 18 (1), Art.-Nr.: e2271455. doi:10.1080/17452759.2023.2271455
Czink, S.; Holoch, J.; Renz, R.; Schulze, V.; Albers, A.; Dietrich, S.
2023. Processes, 11 (3), 648. doi:10.3390/pr11030648
Englert, L.; Klumpp, A.; Ausländer, A.; Schulze, V.; Dietrich, S.
2022. Additive Manufacturing Letters, 3, Article no: 100067. doi:10.1016/j.addlet.2022.100067
Czink, S.; Dietrich, S.; Schulze, V.
2022. NDT & E International, 132, Article no: 102729. doi:10.1016/j.ndteint.2022.102729
Damon, J.; Czink, S.; Schüßler, P.; Antusch, S.; Klein, A.; Send, S.; Dapprich, D.; Dietrich, S.; Schulze, V.
2022. Materials Science and Engineering: A, 849, Art.-Nr. 143422. doi:10.1016/j.msea.2022.143422
Li, H.; Hu, Y.; Di, R.; Yuan, R.; Shi, C.; Lei, J.
2022. Ceramics International, 48 (14), 20388–20399. doi:10.1016/j.ceramint.2022.03.324
Shi, C.; Dietrich, S.; Schulze, V.
2022. The International Journal of Advanced Manufacturing Technology, 121 (3-4), 1899–1913. doi:10.1007/s00170-022-09474-9
Klumpp, A.; Ruf, M.; Dietrich, S.; Schulze, V.
2022. Engineering Fracture Mechanics, 269, Art.-Nr.: 108551. doi:10.1016/j.engfracmech.2022.108551
Mühl, F. A.
2022, May 13. Karlsruher Institut für Technologie (KIT). doi:10.5445/IR/1000145728
Lingelbach, Y.; Waldenmaier, T.; Hagymasi, L.; Mikut, R.; Schulze, V.
2022. Materialwissenschaft und Werkstofftechnik, 53 (5), 576–589. doi:10.1002/mawe.202100249
Bayoumy, D.; Kwak, K.; Boll, T.; Dietrich, S.; Schliephake, D.; Huang, J.; Yi, J.; Takashima, K.; Wu, X.; Zhu, Y.; Huang, A.
2022. Journal of materials science & technology, 103, 121–133. doi:10.1016/j.jmst.2021.06.042
Nouri, N.; Li, Q.; Damon, J.; Mühl, F.; Graf, G.; Dietrich, S.; Schulze, V.
2022. Journal of Materials Research and Technology, 18, 931–942. doi:10.1016/j.jmrt.2022.02.126
Damon, J. M.
2022, January 27. Karlsruher Institut für Technologie (KIT). doi:10.5445/IR/1000142202
Jiao, T.; Chen, X.; Lei, J.; Shi, C.; Liu, G.
2022. Journal of Materials Engineering and Performance, 32 (13), 6072–6082. doi:10.1007/s11665-022-07517-6
Li, H.; Xia, Y.; Xie, M.; Shi, C.; Lei, J.
2022. Journal of Alloys and Compounds, 929, Art.-Nr.: 167261. doi:10.1016/j.jallcom.2022.167261
Schulze, V.; Bleicher, F.; Courbon, C.; Gerstenmeyer, M.; Meier, L.; Philipp, J.; Rech, J.; Schneider, J.; Segebade, E.; Steininger, A.; Wegener, K.
2022. CIRP Journal of Manufacturing Science and Technology, 38, 139–158. doi:10.1016/j.cirpj.2022.04.008
Englert, L.; Heuer, A.; Engelskirchen, M. K.; Frölich, F.; Dietrich, S.; Liebig, W. V.; Kärger, L.; Schulze, V.
2022. Virtual and Physical Prototyping, 17 (3), 508–527. doi:10.1080/17452759.2022.2048228
Englert, L.; Schulze, V.; Dietrich, S.
2022. Materials, 15 (3), Art.-Nr.: 1105. doi:10.3390/ma15031105
Englert, L.; Czink, S.; Dietrich, S.; Schulze, V.
2022. Journal of materials processing technology, 299, Art.-Nr.: 117331. doi:10.1016/j.jmatprotec.2021.117331
Damon, J. M.; Dietrich, S.; Schulze, V.
2021. HTM - journal of heat treatment and materials, 76 (6), 458–477. doi:10.1515/htm-2021-0021
Hemmesi, K.; Holey, H.; Elmoghazy, A.; Böhm, R.; Farajian, M.; Schulze, V.
2021. Materials Science and Engineering A, 824, Art.-Nr.: 140826. doi:10.1016/j.msea.2021.140826
Damon, J. M.; Pulvermacher, S.; Dietrich, S.; Schulze, V.
2021. HTM - journal of heat treatment and materials, 76 (4), 273–297. doi:10.1515/htm-2021-0009
Mühl, F.; Knoll, M.; Khabou, M.; Dietrich, S.; Groche, P.; Schulze, V.
2021. Advances in industrial and manufacturing engineering, 2, Art.-Nr. 100039. doi:10.1016/j.aime.2021.100039
Karapuzha, A. S.; Fraser, D.; Schliephake, D.; Dietrich, S.; Zhu, Y.; Wu, X.; Huang, A.
2021. Journal of alloys and compounds, 862, Art.-Nr.: 158034. doi:10.1016/j.jallcom.2020.158034
Damon, J. M.; Surm, H.; Saddei, P.; Dietrich, S.; Schulze, V.
2021. HTM - journal of heat treatment and materials, 76 (1), 36–57. doi:10.1515/htm-2020-0003
Hamm, M.; Bongers-Loth, M. D.; Roddatis, V.; Dietrich, S.; Pundt, A.
2021. 17th International Conference on Diffusion in Solids and Liquids (DSL 2021), Valletta, Malta, June 28–July 2, 2021
Graf, G.; Nouri, N.; Dietrich, S.; Zanger, F.; Schulze, V.
2021. Materials, 14 (15), Art.-Nr.: 4251. doi:10.3390/ma14154251
Klumpp, A.; Kauffmann, A.; Seils, S.; Dietrich, S.; Schulze, V.
2021. Metallurgical and materials transactions / A, 52, 4331–4341. doi:10.1007/s11661-021-06371-w
Damon, J. M.; Jung, E.; Zürn, M.; Dietrich, S.; Schulze, V.
2021. Powder metallurgy, 64 (4), 262–272. doi:10.1080/00325899.2021.1901027
Hunkel, M.; Dong, J.; Epp, J.; Kaiser, D.; Dietrich, S.; Schulze, V.; Rajaei, A.; Hallstedt, B.; Broeckmann, C.
2020. Materials, 13 (22), Art.-Nr.: 5058. doi:10.3390/ma13225058
Bayoumy, D.; Schliephake, D.; Dietrich, S.; Wu, X. H.; Zhu, Y. M.; Huang, A. J.
2020. Materials and design, 198, Art.Nr. 109317. doi:10.1016/j.matdes.2020.109317
Mühl, F.; Damon, J.; Dietrich, S.; Schulze, V.
2020. Computational materials science, 184, Art. Nr.: 109916. doi:10.1016/j.commatsci.2020.109916
Mühl, F.; Jarms, J.; Kaiser, D.; Dietrich, S.; Schulze, V.
2020. Materials and design, 195, Art.Nr. 108964. doi:10.1016/j.matdes.2020.108964
Englert, L.; Dietrich, S.; Pinter, P.
2020. Rapid prototyping journal, 26 (9), 1603–1614. doi:10.1108/RPJ-07-2019-0200
Damon, J.; Dietrich, S.; Schulze, V.
2020. Journal of materials research and technology, 9 (4), 8245–8257. doi:10.1016/j.jmrt.2020.05.035
Kaiser, D.; Damon, J.; Mühl, F.; Graaff, B. de; Kiefer, D.; Dietrich, S.; Schulze, V.
2020. Journal of materials processing technology, 279, Article no: 116485. doi:10.1016/j.jmatprotec.2019.116485
Mühl, F.; Klug, M.; Dietrich, S.; Schulze, V.
2020. Processes, 8 (10), Art.-Nr.: 1303. doi:10.3390/pr8101303
Holoch, J.; Czink, S.; Spadinger, M.; Dietrich, S.; Schulze, V.; Albers, A.
2020. Industrie 4.0 Management, 36 (4), 45
Pinter, P.; Baumann, S.; Lohr, C.; Heuer, A.; Englert, L.; Weidenmann, K. A.
2020. 29th Annual International Solid Freeform Fabrication Symposium - An Additive Manufacturing Conference, SFF 2018; The University of Texas in Austin, United States; 13 August 2018 through 15 August 2018, 2219–2227, Univ. of Texas
Dietrich, S.; Englert, L.; Pinter, P.
2020. 29th Annual International Solid Freeform Fabrication Symposium - An Additive Manufacturing Conference, SFF 2018; The University of Texas in Austin; United States; 13 August 2018 through 15 August 2018, 241–250, Univ. of Texas
Kaiser, D.; Torres-Velasquez, D.; Dietrich, S.; Schulze, V.
2020. Thermochimica acta, 689, Art.Nr. 178612. doi:10.1016/j.tca.2020.178612
Plessis, A. du; Roux, S. G. le; Waller, J.; Sperling, P.; Achilles, N.; Beerlink, A.; Métayer, J.-F.; Sinico, M.; Probst, G.; Dewulf, W.; Bittner, F.; Endres, H.-J.; Willner, M.; Drégelyi-Kiss, Á.; Zikmund, T.; Laznovsky, J.; Kaiser, J.; Pinter, P.; Dietrich, S.; Lopez, E.; Fitzek, O.; Konrad, P.
2019. Additive manufacturing, 30, Art.-Nr. 100837. doi:10.1016/j.addma.2019.100837
Hamm, M.; Bongers, M. D.; Roddatis, V.; Dietrich, S.; Lang, K.-H.; Pundt, A.
2019. International journal of hydrogen energy, 44 (60), 32112–32123. doi:10.1016/j.ijhydene.2019.10.057
Damon, J.; Hanemann, T.; Dietrich, S.; Graf, G.; Lang, K.-H.; Schulze, V.
2019. International journal of fatigue, 127, 395–402. doi:10.1016/j.ijfatigue.2019.06.025
Damon, J.; Dietrich, S.; Gorantla, S.; Popp, U.; Okolo, B.; Schulze, V.
2019. Rapid prototyping journal, 25 (7), 1319–1327. doi:10.1108/RPJ-01-2019-0002
Damon, J.; Koch, R.; Kaiser, D.; Graf, G.; Dietrich, S.; Schulze, V.
2019. Additive manufacturing, 28, 275–284. doi:10.1016/j.addma.2019.05.012
Hanemann, T.; Carter, L. N.; Habschied, M.; Adkins, N. J. E.; Attallah, M. M.; Heilmaier, M.
2019. Journal of alloys and compounds, 795, 8–18. doi:10.1016/j.jallcom.2019.04.260
Kiefer, D.; Schüssler, P.; Mühl, F.; Gibmeier, J.
2019. HTM - journal of heat treatment and materials, 74 (1), 23–35. doi:10.3139/105.110374
Kaiser, D.; Charlet-Berguerand, H.; Dietrich, S.; Schulze, V.
2019. HTM - journal of heat treatment and materials, 74 (4), 228–237. doi:10.3139/105.110384
Cheng, W.; Outeiro, J.; Costes, J.-P.; M’Saoubi, R.; Karaouni, H.; Dietrich, S.; Marcon, B.; Rosa, P.
2019. Procedia CIRP, 82, 374–378. doi:10.1016/j.procir.2019.04.057
Segebade, E.; Gerstenmeyer, M.; Dietrich, S.; Zanger, F.; Schulze, V.
2019. Procedia CIRP, 82, 113–118. doi:10.1016/j.procir.2019.04.043
Muehl, F.; Dietrich, S.; Schulze, V.
2019. HTM - journal of heat treatment and materials, 74 (3), 191–201. doi:10.3139/105.110382
Dollhofer, B.; Damon, J.; Scholz, J.; Popp, U.; Dietrich, S.; Okolo, B.
2018. DDMC 2018 : Fraunhofer Direct Digital Manufacturing Conference : proceedings : Direct Digital Manufacturing Conference, Berlin, March 14-15, 2018, 77–80, Fraunhofer Verlag
Albers, A.; Holoch, J.; Dietrich, S.; Spadinger, M.
2018. Exploring the Design Freedom of Additive Manufacturing through Simulation, Helsinki, FIN, December 10-11, 2018, 62–63
Kaiser, D.; Graaff, B. de; Dietrich, S.; Schulze, V.
2018. (F. Delaunois, V. Vitry & F. Roudet, Eds.) Metallurgical research & technology, 115 (4), Art. Nr.: 404. doi:10.1051/metal/2018026
Damon, J.; Mühl, F.; Dietrich, S.; Schulze, V.
2018. Metallurgical and materials transactions / A, 1–14. doi:10.1007/s11661-018-5004-6
Klumpp, A.; Maier, S.; Chen, H.; Fotouhi, M.; Schneider, R.; Dietrich, S.; Lang, K.-H.; Schulze, V.
2018. International journal of fatigue, 116, 257–267. doi:10.1016/j.ijfatigue.2018.06.033
Damon, J.; Dietrich, S.; Vollert, F.; Gibmeier, J.; Schulze, V.
2018. Additive manufacturing, 20, 77–89. doi:10.1016/j.addma.2018.01.001
Kaiser, D.; Graaff, B. de; Jung, A. M.; Dietrich, S.; Schulze, V.
2017. Materials science and engineering / A, 705, 114–121. doi:10.1016/j.msea.2017.08.028
Klumpp, A.; Lienert, F.; Dietrich, S.; Soyama, H.; Schulze, V.
2017. ICSP13 : 13th International Conference on Shot Peening : 18-21 September 2017, Montréal, Canada., 441–446, Polytechnique Montréal
Klumpp, A.; Tamam, M.; Vollert, F.; Dietrich, S.; Schulze, V.
2017. ICSP13 : 13th International Conference on Shot Peening : 18-21 September 2017, Montréal, Canada, 435–440, Montreal
Hofmann, A.; Thißen, E.; Migeot Matthias; Bohn, N.; Dietrich, S.; Hanemann, T.
2017. Polymers, 9 (10), 489/1–12. doi:10.3390/polym9100489
Weidenmann, K. A.; Dietrich, S.; Grigo, M.; Elsner, P.
2017. 21st Symposium on Composites, 2017; Bremen; Germany; 5 July 2017 through 7 July 2017. Ed.: A. S. Herrmann, 3–8, Trans Tech Publications. doi:10.4028/www.scientific.net/KEM.742.3
Grell, D.; Gibmeier, J.; Dietrich, S.; Silze, F.; Böhme, L.; Schulze, V.; Kühn, U.; Kerscher, E.
2017. Surface engineering, 33 (9), 721–730. doi:10.1080/02670844.2017.1282712
Klumpp, A.; Tamam, M.; Lienert, F.; Dietrich, S.; Gibmeier, J.; Schulze, V.
2016. Materials research proceedings, 175–180. doi:10.21741/9781945291173-30
Kaiser, D.; Graaff, B. de; Dietrich, S.; Schulze, V.
2016. Thermochimica acta, 646, 8–15. doi:10.1016/j.tca.2016.10.014
Habschied, M.; Dietrich, S.; Heussen, D.; Schulze, V.
2016. HTM - journal of heat treatment and materials, 71 (5), 212–217. doi:10.3139/105.110294
Klumpp, A.; Lienert, F.; Dietrich, S.; Schulze, V.
2015. Proceedings : 5th International Conference on Distortion Engineering 2015, Bremen, Germany, 23 - 25 September 2015 / eds. H.-W. Zoch, Th. Lübben ; organised by IWT, 105–115, IWT
Merzkirch, M.; Pinter, P.; Dietrich, S.; Weidenmann, K. A.
2015. 20th Symposium on Composites, Vienna, Austria, July 1-3. Ed.: Ch. Edtmaier, 109–116, Trans Tech Publications. doi:10.4028/www.scientific.net/MSF.825-826
Moch, K.; Dietrich, S.; Schulze, V.
2015. Heat treatment and surface engineering: from tradition to innovation : European Conference on Heat Treatment 2015 & 22nd IFHTSE congress ; Venice (Italy), 20 - 22 May 2015, CD-ROM, AIM
Erz, A.; Klumpp, A.; Hoffmeister, J.; Schulze, V.
2014. ICSP12 : proceedings of the 12th International Conference on Shot Peening : Goslar, Germany, September 15-18, 2014 / editor Lothar Wagner, Chairman of ICSP-12, Institute of Materials Science and Engineering, Clausthal University of Technology, Germany, 353–358, Lothar Wagner
Klumpp, A.; Hoffmeister, J.; Schulze, V.
2014. ICSP12 : proceedings of the 12th International Conference on Shot Peening : Goslar, Germany, September 15-18, 2014 / editor Lothar Wagner, Chairman of ICSP-12, Institute of Materials Science and Engineering, Clausthal University of Technology, Germany, 12–24, Lothar Wagner