Research
We contribute to KIT division III "Mechanical and Electrical Engineering".
Our activities for large scale research are focused on the Helmholtz program Materials and Technologies for the Energy Transition (MTET).
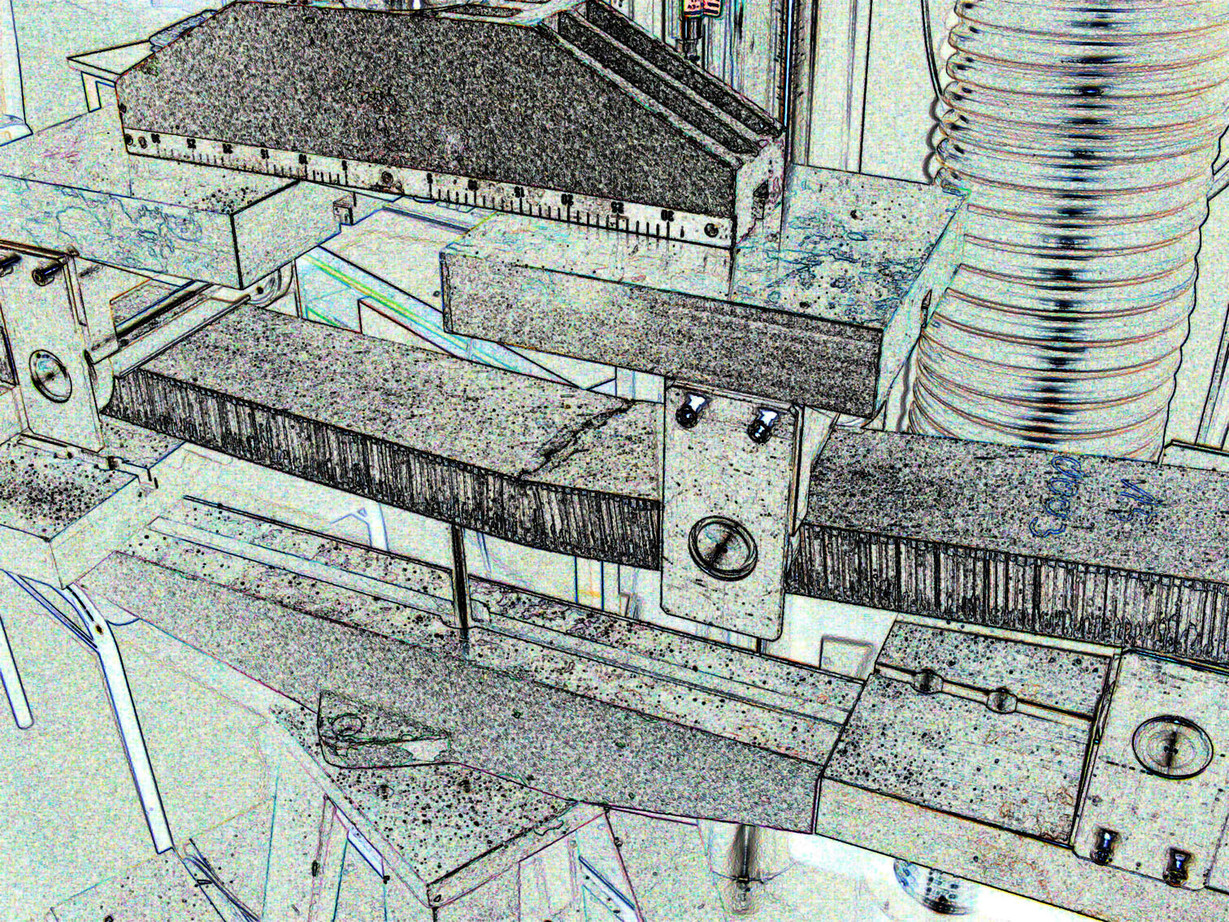
Hybrid materials, i.e. composites or compounds, made or joint from several materials play a very important role in industrial application. The aim of hybrid lightweight construction is the mass reduction of lightweight structures and simultaneously the increase of performance of the construction, which is reflected in higher strength, stiffness or improved fatigue strength. In addition to steels with a comparably high stiffness and density both light metals like aluminium and magnesium as well as polymers feature a high potential for lightweight construction due to their low density. One major advantage of the last-mentioned material class is furthermore the excellent processability. A disadvantage of all lightmetals and polymers is the low stiffness which may be increased by reinforcements like ceramic or metallic fibres or particles increasing both absolute and specific stiffness. The combination of different materials in compounds or composites results in the evolution of an interface which is essential for the composite's performance as it provides the internal load transfer between the composite's components.
more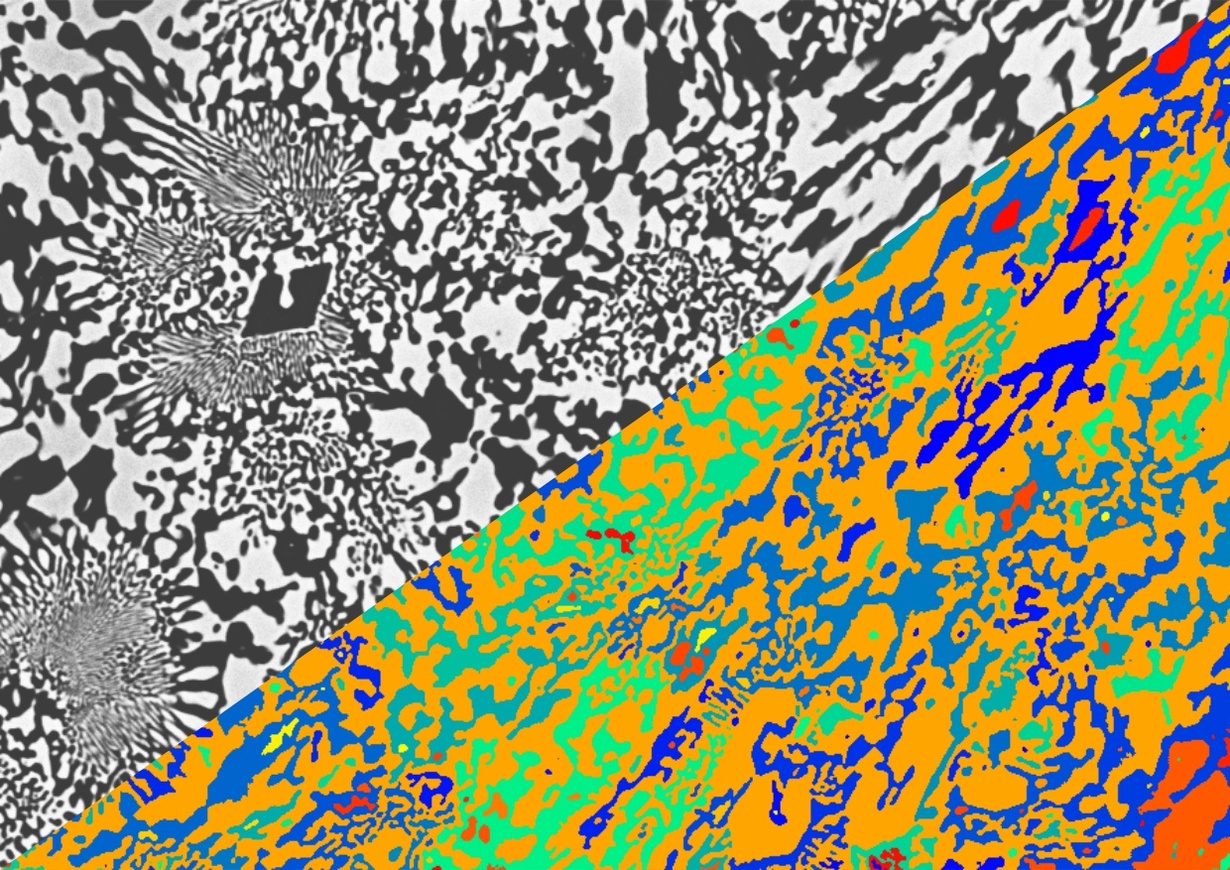
The Physical Metallurgy group focuses on the development of metallic and intermetallic materials for harsh environments. The investigation and optimization of materials for engines operating at high temperatures is of central interest. Therefore, outstanding high temperature stability (mechanical and microstructural) in conjunction with reasonable toughness at room temperature as well as suitable oxidation resistance are the main objectives of the research. In addition, fundamentals of contact materials for vacuum switches and the deformation behavior of high-entropy alloys under various conditions are studied in detail.
more
The research and development work of the "Materials and Processes" department is embedded in the program-oriented funding of the large-scale research part of the Helmholtz Association. The R&D work is spread across the following research programs Materials and Technologies for the Energy Transition (MTET), Fusion and Materials Systems Engineering (MSE).
more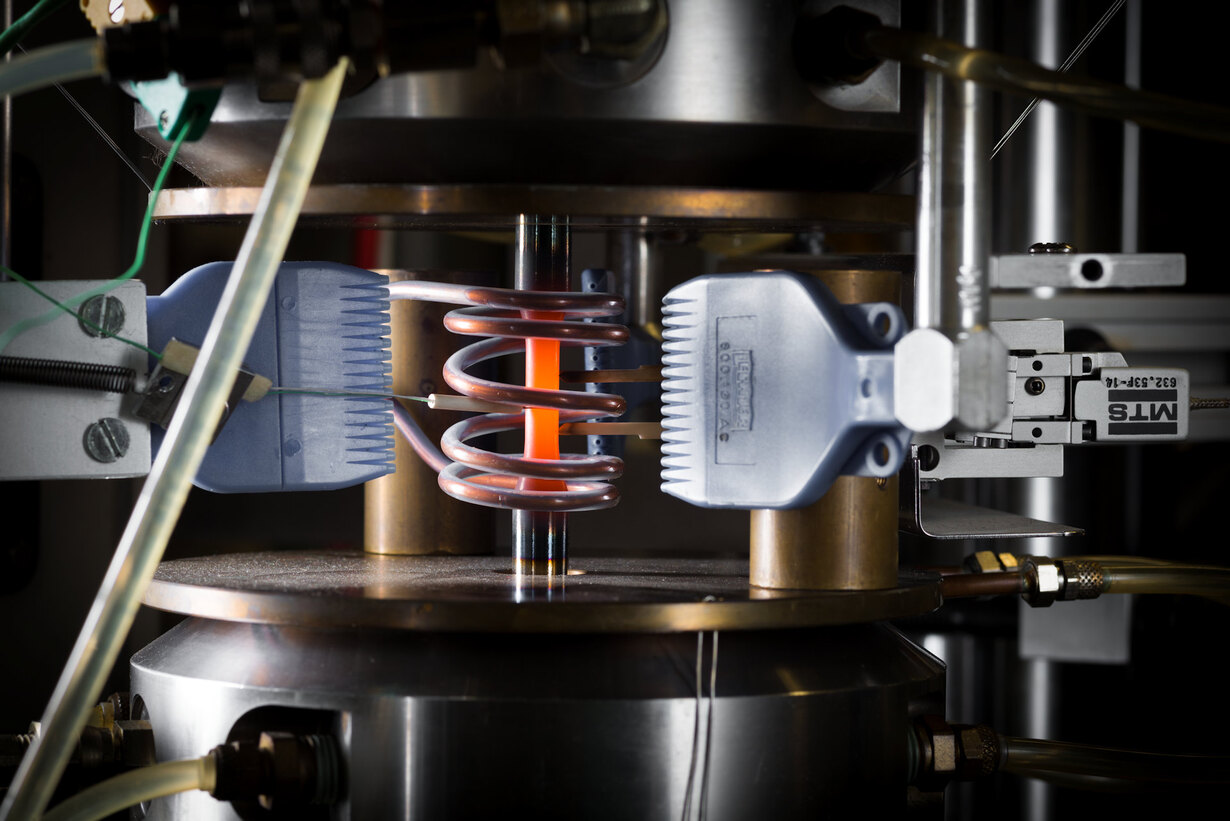
The fatigue group deals with testing, assessment and optimisation of materials under cyclic loading. For this purpose, fatigue tests under push-pull, bending, torsion and superimposed loading are conducted at room and elevated temperature. Further, we perform thermo-mechanical fatigue tests, where temperature and mechanical load are cycled simultaneously to simulate the conditions in hot going components (e. g. cylinder heads or turbine blades). Depending on the loading conditions the lifetime of the tested specimens extends from a few hundred to 109 cycles. The objective is to better understand the damage mechanisms acting under the particular loading conditions and based on this to develop models for lifetime prediction and to optimise the material state for the respective load.
more
In the framework of the research of the section "Production and Component Behaviour" the interactions between production processes, component state and component behaviour at mechanical loading are investigated. The production processes considered are available either in the laboratories of production techniques of IAM-WK or within cooperations with institutes of production sciences.
more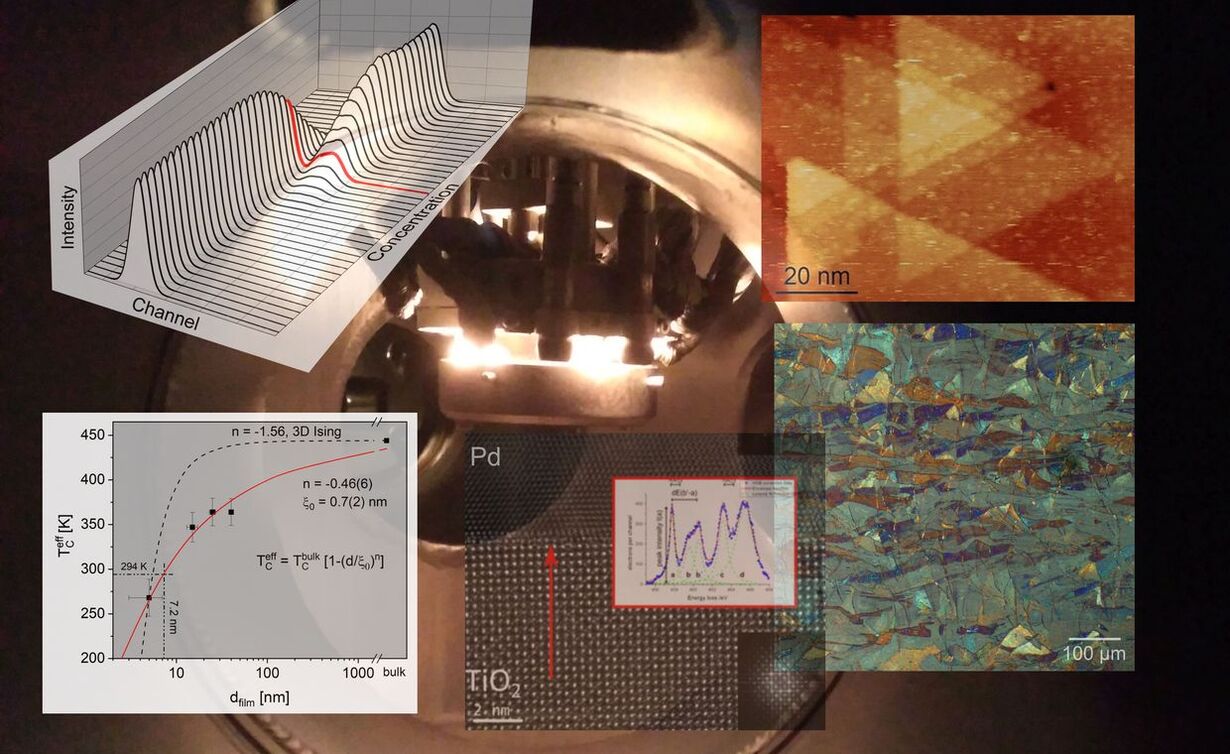
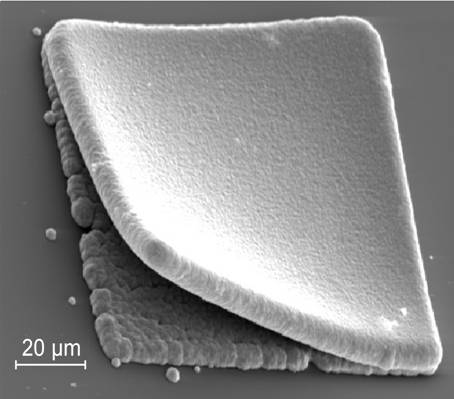
The Structure and Stress Analysis group focuses on the physical metallurgy of metal/ceramic composites and of two-phase alloys, the analysis of residual stresses in structural components, especially in mechanically treated edge zones, the development and application of advanced nondestructive techniques for materials characterization using X-rays or ultrasonic waves.
more